Is Non-Combustibility Good for your Health?
In the wake of Grenfell tower disaster in London, an out of cycle amendment was made to the building code to increase fire safety of façade systems. A new provision was included in March 2018 to combine a series of requirements and concessions for non-combustible building elements. The key change was to tighten up requirements for the use of combustible materials in façade systems. The added clause C1.9 as part of a deemed-to-satisfy solution requires apartments with 2 or more stories to have non-combustible external walls, including all components incorporated in them; façade coverings, framing and insulation. AS 1530.1 is the material combustibility test in which a small sample of product is placed into a furnace and if any increase in temperature in the furnace is detected the sample is considered to be giving off heat (i.e. undergoing a combustion reaction), and therefore deemed a combustible material.
This has given rise to a wave of multi-residential developments which are utilising lightweight steel framing external walls with metal sheathing (non-combustible) as the primary water barrier that sits behind the decorative (non-combustible) cladding system. These systems utilise metal materials that meet the non-combustibility requirement for a deemed-to-satisfy solution but potentially raise a more insidious problem with moisture accumulation.
Metal sheathing is a perfect vapour barrier and these wall systems create a high risk of trapping moisture. Here’s why:
- The apartments become relatively well sealed. This is because the metal sheathing acting as a water barrier needs to be sealed to prevent driving rain entering into the insulation systems. The metal sheathings primary purpose is a wind/water barrier for weatherisation.
- The building code relies on operable windows and occupants using them to purge moisture in winter. This may or may not happen as intended and is an ongoing debate.
- The indoor humidity within the apartments increases in the colder months of the year due to the more well sealed structure and inadequate controlled ventilation strategies. Humidity in apartments above 80% RH is not uncommon which was a hot topic of discussion at the 2018 AIRAH Building Physics Forum.
- External cladding will become cold in winter and at night due to re-radiation of heat back to the night sky.
- The metal sheathing that sits behind the external cladding also becomes cold.
- The fibrous insulation and the plasterboard on the inside are generally highly water vapour permeable and the plasterboard also contains sockets and power points.
- Water vapour from occupants cooking, cleaning, bathing etc. can migrate into the structure through the interior plasterboard and the fibrous insulation to reach the back of the cold metal sheathing where it can create condensation and moisture accumulation.
The long-term health and durability of the structure may be compromised by inducing mould growth and/or corrosion of the structure.
Professor Hartwig Künzel from Fraunhofer Institute for Building Physics recently presented a keynote at the AIRAH Building Physics Forum on the 22nd of November 2018 which highlighted this exact issue.
The strategies to mitigate the long-term consequences of moisture accumulation in insulated structures range from additional vapour control air barriers on the inside of the structure to prevent moisture reaching the external back pan to a combination of external vapour permeable, water and wind barriers (“sarking”) that allow the water vapour to dry to the outside ventilated cavity. Options presented by Professor Künzel are shown in Table 1.
Table 1. Options for moisture control in the exterior building envelope of steel framed apartments.
But what works where is dependent on one critical factor…the climate where you are building!
Professor Künzel presented an analysis on internal and external control layer solutions at the AIRAH Building Physics Forum in which he tested 10 cities across Australia using WUFI® software to asses vapour diffusion flows and moisture content in the 5mm glass wool layer behind the metal sheathing.
Figure 1. Climates analysis presented by Professor Künzel for moisture accumulation at AIRAH Building Physics Forum 2018; Adelaide, Brisbane, Cairns, Canberra, Darwin, Hobart, Melbourne, Perth, Sydney
The key driver of moisture being trapped behind vapour impermeable sheathings (metal) is the interior humidity in the living space. With modern apartments they can be relatively well sealed and the building code does not require controlled (mechanical) ventilation to purge this moisture. The American Society for Heating Refrigeration and Air Conditioning Engineers (ASHRAE) have developed a standard (ASHRAE 160) that utilises key parameters for predicting the internal conditions. This includes the air tightness, the occupancy (moisture generation rate), and the volume of the space. As one would expect, air tight buildings with high occupancy and small volume will have high internal humidity as shown in Figure 2. As presented by Professor Künzel at the Australian Institute for Refrigeration and Heating (AIRAH) Building Physics Forum 2018 these algorithms result in relative humidity as high as 70% in the heating season in nearly all Australian climates. I observed that many engineers who attended the AIRAH Building Physics Forum suggested this resonated with their experience.
Figure 2. Assumed internal humidity conditions according to ASHRAE 160, 100m2 Apartment, 3 bedrooms (4 occupants); an average air change rate of 0.2 h-1
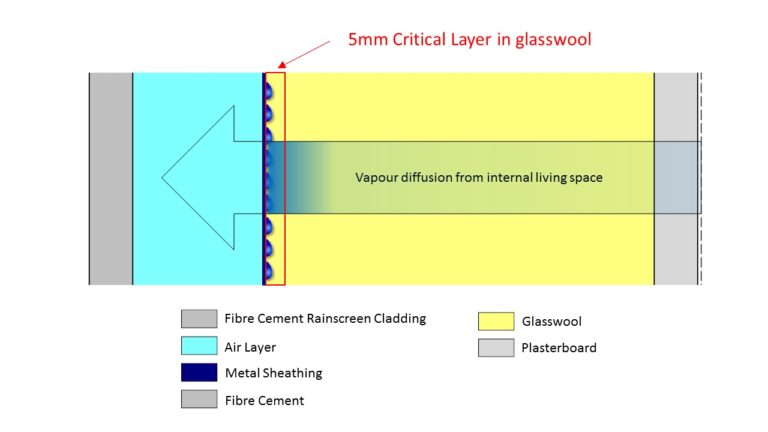
High humidity within the interior living space of apartments may become a health and durability issue as a consequence of fire safety stringency increases. The fundamental issue is that the water vapour diffuses outwards towards the metal sheathing material which then causes high humidity and consequential condensation behind the metal sheathing layer.
Professor Künzel highlighted the moisture content in the outer most 5mm glasswool layer in which the analysis found extremely high-water content (potential accumulation of condensation). The process is shown in Figure 3.
Outward vapour drive in residential apartments with high internal humidity can cause condensation on the back side of metal sheathing materials. Interestingly in tropical climates Künzel found that a metal sheathing may actually be beneficial in preventing water vapour entering in to the structure in tropical climates.
In this case, he suggested a metal back pan may not be such a bad idea in air-conditioned apartments in Darwin and Cairns, but has significant issues in Hobart, Canberra and Melbourne and signs of moisture accumulation in Adelaide, Perth, Sydney, Alice Springs and Brisbane. See Figure 4 for water present in the outer 5mm layer of glasswool per m2 of façade.
Figure 4. Moisture content in outer 5mm glasswool with a metallic external sheathing on a south facing wall.
With a vapour permeable fibre cement sheathing and vapour permeable SOLITEX EXTASANA ADHERO® applied over the top, it is possible to release the water vapour by diffusion into the ventilation cavity so that it is safely ventilated away. Professor Künzel indicated this is suitable in many climates but the coldest regions of Australia, Canberra, Hobart and Melbourne still present a moisture accumulation issue, see Figure 5. Professor Künzel highlighted in tropical climates, such as Darwin and Cairns, it may be necessary to undertake further analysis of the internal plasterboard in this case to ensure that the water vapour does not create high humidity at the internal air-conditioned plasterboard surface and consequential mould growth. In this case it may be preferable to have higher vapour resistance on the outside water/air barrier (“sarking”).
Figure 5. Moisture content in outer 5mm glass wool with a fibre cement external sheathing and pro clima SOLITEX EXTASANA ADHERO® on a south facing wall.
If water vapour can be prevented from entering in to the structure it is possible to limit the moisture accumulation, even behind a metal sheathing. A well implemented pro clima INTELLO® membrane does just this. It prevents the water vapour from reaching the metal sheathing and can reduce the chance of moisture accumulation behind the metal sheathing significantly, but still presents a risk as shown by Professor Künzel in Figure 6.
Figure 6. Moisture content in outer 5mm glass wool with a metal sheathing and pro clima INTELLO® membrane on a south facing wall.
With a vapour permeable external sheathing and vapour permeable SOLITEX EXTASANA ADHERO® applied over and an INTELLO® as an internal vapour control layer, the risk of moisture accumulation in the outer 5mm glasswool is eliminated in all climates. In this case Professor Künzel highlighted that in tropical climates, like Darwin and Cairns, further analysis would be required to see what happens in the 5mm glasswool layer adjacent to INTELLO®. This is because the situation reverses due to the extreme external humidity in the tropics where moisture could drive inwards and accumulate behind the internal plasterboard. The metal back pan solution is likely to provide suitable vapour control in those two climates.
Figure 7. Moisture content in outer 5mm glass wool with a fibre cement external sheathing and pro clima SOLITEX EXTASANA ADHERO® and pro clima INTELLO® on a south facing wall.
Pro Clima products are designed to manage external driving rain, internal humidity entering the structure and increase the drying capacity of systems for healthy, durable and well-insulated building envelopes. Figures 8. to 11. below describe options for implementation of moisture management in steel frame apartments.
Figure 8. Metal sheathing (“Back Pan”) solution which has been driven by fire code requirements.
Figure 9. A rigid fibre cement wind brace and SOLITEX EXTASANA ADHERO® water/air barrier solution.
Figure 10. Metal sheathing (“Back Pan”) can be enhanced by the use of INTELLO® to prevent water vapour reaching the metal sheathing.
Figure 11. A rigid fibre cement wind brace and SOLITEX EXTASANA ADHERO® water/air barrier solution can be enhanced by the use of INTELLO® to manage internal water vapour and allow drying to the ventilated cavity.
It is likely that the 2019 BCA will be addressing this particular issue through a new section in the building code “condensation management.” The verification pathway allows a calculation of the moisture accumulation based on the indoor and outdoor conditions along with the material properties selection to prove that moisture will not accumulate within the structure leading to long term consequences. Pro Clima can work with you on solutions for any building in any climate.
Tags In
Authors
Recent articles
- German School Buildings Top The Class November 21, 2024
- The Perfect Pod July 24, 2024
- Above Sheathing Ventilation – Part 0: Flat Roofs September 12, 2023
- Above Sheathing Ventilation – Part 3: Fighting the Sun December 13, 2021
- Above Sheathing Ventilation – Part 2: The Blue Planet October 26, 2021